1、常用的涂装方法介绍
(1)流化床浸涂法:
流化床浸涂法是将预热的工件浸入已被流化的粉末容器中,使粉末熔融附着到工件上,然后再将工件置于烘箱或烤炉中烘烤。工件的预热温度要高于粉末的熔融温度,但应低于粉末的分解温度,一次涂装可达200um以上。该方法设备简单,无需回收装置,粉末利用率高,能100%加以利用,但涂层不太均匀,不能薄涂,难以涂装结构复杂的大型工件,工件须预热,热能损耗大。
该涂装方法适于小型工件,如马达定子、异型管、阀门、冰箱货架、鸟笼、自行车货篮等的涂装。也有部分较大型工件如金属护栏和护网采用该法涂装。
(2)火焰喷涂法:
粉末涂料通过高温火焰气体而熔融,并被喷涂到工件上,经流平交联固化而成涂膜。该方法不需要烤箱或烘道,可现场涂装,可厚涂至500um以上。该方法适用的粉末品种较少,主要用来喷涂热塑性粉末,如乙烯-乙酸乙烯共聚物(eva)、聚乙烯、聚酰胺等。
(3)静电粉末涂装法:
利用高压电场效应,使粉末和工件受感应而分别带上彼此相反的电荷,粉末吸附到工件上去。该方法是当前最主要的粉末涂装加工方法,能适应几乎所有品种粉末的涂装。其带电方式有两种:高压静电和摩擦带电。
(4)静电流化床浸涂法:
这是一种将流化床浸涂法和静电粉末喷涂法相结合的涂装工艺。工件不用预热,粉末利用率高,易实现自动化生产。
(5)真空吸引涂装法:
该方法适用于喷涂小口径管道。
(6)电场云涂装法:
这是最新开发的一种涂装工艺,也属静电喷涂,它用瞳定的喷嘴和平行排列的电极代替了通常的活动式喷枪。经压缩空气吹出的粉末被送入电极空间,通过电晕针产生的离子而使之带电,这就是电场云。接地工件进入电场云,在电晕针和工件之间形成电场,使带电粉末吸附到工件上,然后通过加热固化完成涂装。该法最大的优点是上粉率可达95%,比一般静电喷涂法节省1/3-1/2粉末,涂层致密平整;现已型发用于pcm(预涂钢板)的生产流水线涂装。
2、静电喷涂原理和种类
(1)高压静电喷涂:
主要采用电晕放电式静电粉末喷枪系统来完成粉末喷涂。该系统包括:1)高压静电发生器(由高频变压器和升压回路组成):2)电晕放电电极(由针状电极和环状电极组成):3)喷束调节器:4)空气和粉末输送管路等。随着喷涂技术的不断发展创新,现已能将高压静电发生器装在喷枪内部。接通低压电源,经多段升压器转换成高压电,施加到喷枪端部的电晕放电电极或环状电极上,使电极周围的空气离子化,并与接地的工件(一般为阳极.带正电)之间形成电场。粉末涂料由压缩空气输送到喷枪前端.雾化喷出,粉末穿过电场时将带上负电荷,在电场力(静电引力)和压缩空气的作用下飞向工件表面,并吸附在工件上。
(2)摩擦静电喷涂:
摩擦静电喷涂的主要原理是两种不同的非导体在相互摩擦时产生正电荷和负电荷,使导体带上静电荷。在粉末涂装工艺中主要采用聚四氟乙烯(ptfe)作为摩擦材料,置于喷枪内壁,当粉末随着压缩空气进入喷管后,由于快速运动而与ptfe剧烈摩擦,粉末与ptfe性能差别很大,从而使粉末粒子带上正电荷,在气流的推力下飞向工件(由于接地而作为阴极),吸附在工件表面,然后经烘烤固化。
3、影响粉末喷涂效率的因素
粉末喷涂的效率有赖于完善的喷涂设备,“工欲善其事,必先利其器”:先进的设备和良好的管理是完成喷涂的先决条件,这里我们先不做讨论。
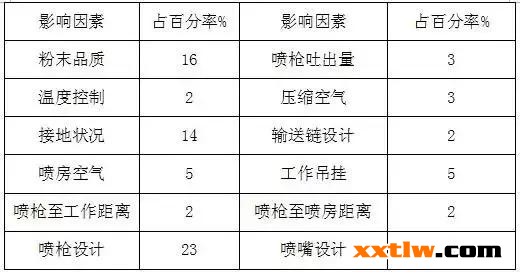
表1 影响粉末喷涂效率的各项因素
曾经一度很多专家都考察过国内数十家中小型粉末生产厂,据专家描述:它们供应的粉末产品质量参差不齐,但都有一个突出的问题——即粉末流动性差,喷涂时粉末一次上粉率很低,回收量大,喷涂效率不易提高。与此相反,一些大企业如杜邦华佳、阿克苏、诺贝尔、ppg等,它们提供的粉末流动性好,上粉率高,具有明显的优势。
那按照粉末生产工艺来分析,国内小粉末厂主要在三个方面与这些大企业存在差距:1)设备:2)生产工艺:3)检测手段。
(2)什么是流动性好的粉末?
流动性好的粉末涂料在使用过程中易于流化,粉体疏松,有流水般的效果,从供粉桶至喷枪的粉末传送轻便,且粉末的雾化效果好,没有结团或吐粉现象。我们曾经用激光粒径分析仪和电子显微镜对众多厂家的粉末涂料进行检测和观察,从中发现了一些规律性的现象,简单归纳如表2。
那按照粉末生产工艺来分析,国内小粉末厂主要在三个方面与这些大企业存在差距:1)设备:2)生产工艺:3)检测手段。
(2)什么是流动性好的粉末?
流动性好的粉末涂料在使用过程中易于流化,粉体疏松,有流水般的效果,从供粉桶至喷枪的粉末传送轻便,且粉末的雾化效果好,没有结团或吐粉现象。我们曾经用激光粒径分析仪和电子显微镜对众多厂家的粉末涂料进行检测和观察,从中发现了一些规律性的现象,简单归纳如表2。
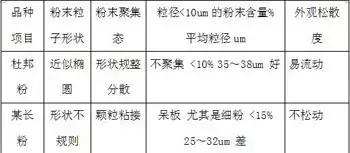
表2 粉末粒子分析比较表
根据经验,生产流动性好的粉末必须注重三点:1)低温粉碎:2)后混流动助剂:3)控制粉末粒径分布:下面将逐一分析。
(3)提高粉末流动性的措施
①低温粉碎
粉末涂料的主要成份是树脂。粉末涂料用树脂的分子量较低,一般只有几千,软化点平均低于120℃.环氧树脂仅为95℃左右,而玻璃化温度(tg)则更低,一般在60"c左右。
现在粉碎粉末涂料绝大多数采用acm磨,粉末的粉碎与分级同时进行,因有大量空气通过磨腔,所以物料和磨体升温幅度小。但在实际使用过程中我们发现,设备长时间运转或在炎热的夏季,粉末的生产效率明显下降,粉末从筛网出来的温度偏高,立即包装后会有松散的结块产生,影响正常使用。这样的粉在电子显微镜下观察,就会出现表2所说的现象,如粉末形状不规则,许多粒子呈锯齿状等。
国产acm磨进风口很短,空气没有经过处理直接进入磨体,而国外acm磨的进风口很长,且空气进入磨体前经过冷却处理,一般在15℃以下,能保证磨出来的粉温度不超过25℃,远低于粉末的tg点。
建议国内制粉设备厂改进进风管,加装冷冻装置。粉末厂则可在acm磨进风口处加装冷却空调或专用冷风机。有许多粉末厂已采用这种方法,效果很好。粉末厂在条件许可的情况下,应让挤出机出来的半成品尽量冷透,不要立即粉碎。
② 后混流动助剂
粉末涂料本身很细,通常颗粒粒径以微米(um)为单位来衡量。粒度分布呈正态分布的粉末,大都有一定的流动性。但粉末自身的流动性很弱,要提高其流动性应在挤出和粉碎的同时加入气相二氧化硅。
加有一定量气相二氧化硅的粉末涂料在电子显微镜下观察,其粉末颗粒之间不粘连,颗粒感强。原因在于粉末粒子之间漂浮或者流动有粒径更细,比重更小的胶体状二氧化硅微粒。
常用的气相二氧化硅有美国卡博特(cabot)的m-5.eh-5和德国迪高莎(degussa)的aerosil200和aerosil972。这些产品的具体技术指标见表3和表4。
(3)提高粉末流动性的措施
①低温粉碎
粉末涂料的主要成份是树脂。粉末涂料用树脂的分子量较低,一般只有几千,软化点平均低于120℃.环氧树脂仅为95℃左右,而玻璃化温度(tg)则更低,一般在60"c左右。
现在粉碎粉末涂料绝大多数采用acm磨,粉末的粉碎与分级同时进行,因有大量空气通过磨腔,所以物料和磨体升温幅度小。但在实际使用过程中我们发现,设备长时间运转或在炎热的夏季,粉末的生产效率明显下降,粉末从筛网出来的温度偏高,立即包装后会有松散的结块产生,影响正常使用。这样的粉在电子显微镜下观察,就会出现表2所说的现象,如粉末形状不规则,许多粒子呈锯齿状等。
国产acm磨进风口很短,空气没有经过处理直接进入磨体,而国外acm磨的进风口很长,且空气进入磨体前经过冷却处理,一般在15℃以下,能保证磨出来的粉温度不超过25℃,远低于粉末的tg点。
建议国内制粉设备厂改进进风管,加装冷冻装置。粉末厂则可在acm磨进风口处加装冷却空调或专用冷风机。有许多粉末厂已采用这种方法,效果很好。粉末厂在条件许可的情况下,应让挤出机出来的半成品尽量冷透,不要立即粉碎。
② 后混流动助剂
粉末涂料本身很细,通常颗粒粒径以微米(um)为单位来衡量。粒度分布呈正态分布的粉末,大都有一定的流动性。但粉末自身的流动性很弱,要提高其流动性应在挤出和粉碎的同时加入气相二氧化硅。
加有一定量气相二氧化硅的粉末涂料在电子显微镜下观察,其粉末颗粒之间不粘连,颗粒感强。原因在于粉末粒子之间漂浮或者流动有粒径更细,比重更小的胶体状二氧化硅微粒。
常用的气相二氧化硅有美国卡博特(cabot)的m-5.eh-5和德国迪高莎(degussa)的aerosil200和aerosil972。这些产品的具体技术指标见表3和表4。

表3 卡博特气相二氧化硅的特性参数 性能代号 m-5 h-5 hs-5 eh-5
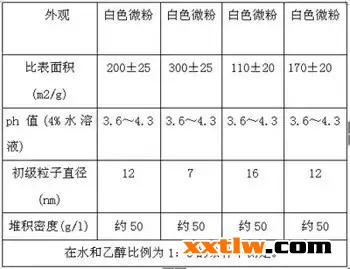
表4 迪高莎气相二氧化硅的特性参数 性能代号 aerosil 200 aerosil 300 aer
气相二氧化硅是四氯化硅通过火焰水解法而得的极细的无定型二氧化硅,为球状微粒,平均粒径7~40nm。气相二氧化硅按极性可分为亲水性和疏水性两类,其中疏水性二氧化硅对改善粉末涂料的工艺应用性很有利,通常在粉碎时添加粉末总量0.1%~0.2%的气相二氧化硅即有理想的效果。如此少的气相二氧化硅对粉末涂料成膜和固化过程中的流动性几乎没有不利影响,有时候还能增加涂膜的边缘包覆能力。但物极必反,过多加入气相二氧化硅将产生不利的作用。从气相二氧化硅的一些物理指标看(可参见表3和表4),胶体状的气相二氧化硅非常细微,以纳米来衡量其直径,具有极强的飞散性,比表面积特别大,很容易飘浮。所以如何准确而定量地将气相二氧化硅加入粉碎机,并与粉末一起粉碎过筛,是一件很困难的工作。
针对国内粉末厂的许多实际情况,这里列出3种使用方法供大家参考。
(1)若仅生产少量的粉末(如几十或一二百公斤),可将预先计算并称量的气相二氧化硅和粉末半成品机械混合——手工或机器搅拌,然后再进行粉碎。
(2)在粉碎机进料段加开进料口,用专门的气相二氧化硅加料机定量地将二氧化硅加入,完成与挤出半成品的共同粉碎。
(3)在acm磨的空气进风口罩上加开进料口,利用负压,将从气相二氧化硅供料机中输出的二氧化硅吸进磨腔里,与挤出半成品一起粉碎。
控制粉末粒径分布
粉末的粗细从宏观角度考虑应是一个统计学概念,因为成品粉末一定是由粗粉、细粉、以及介于粗粉和细粉之间的粉末构成的。粉末粒径以微米(um)为统计单位,早先采用筛分法进行测定。即称取一定质量的粉末,经过叠加在一起的不同粒径的筛网,统计通过各层筛网的粉末质量,以此来表述该粉末的粒径分布状况。筛分法很费时,每次测试至少要耗时一刻钟,重复性差,数据波动大,现在粉末行业已不再推荐使用。
随着技术的进步,激光衍射粒度分析法已日臻成熟,在国外很早即被用来测试粉末涂料的粒径分布。激光衍射粒度分析法快速方便,可在线检测,通常完整测试一个样品粉仅需2~3min,并能在一个图表中表述一组或几组重要参数和粒径分布曲线图,非常直观。
粉末的粒径分布理论上应呈正态分布(即高斯曲线),反映在图上就是在某个中心点两侧粉末的粒径均匀地减少或增大,在中心点处峰值明显,而且必须是单峰分布。通俗地讲,粉末的粒子大小应尽量集中在平均粒径周围,过粗和过细的粉末粒子都应很少。
粉末的粒径分布从测试图表上来分析应注重以下几点。
(1)平均粒径一般以dv 50表示,这是一个统计概念.即将粉末都看成是一个个直径相等的圆球,其直径的数值以微米(um)为计量单位。
(2)细粉含量也是一个统计数字,意思是小于某个粒径的粉末的累计体积占整个粉末粒子体积的百分比,主要考虑小于10um粒子的百分含量。
(3)粗粉含量同样是统计数字,与细粉含量相对应,主要考虑大于90um粒子的粉末含量
(4)图形分布状况,须观察是单峰还是双峰,峰形高耸还是平坦等。
根据实际经验,这里提供常规粉末的粒径分布参数。
(1)高压静电喷枪用粉末:dv50=35~38um。小于10um的细粉<8%,大于90um的粗粉<3%。
(2)摩擦枪用粉末:dv50=40~45um,<10um的细粉含量<6%,<70 um的粗粉含量>90%。
(3)流化床用粉末:dv50一般在50~60um。<10um的、细粉含量<4%,>170um的粗粉含量<3%。
粉末涂料的喷涂性与细粉含量有很大的关系,细粉(尤其是<5um的超细粉)的带电性能非常差,有时干脆就无法带上电荷。所以这一部分粉末通常会进入回收系统而成为直接的损耗。
曾经测试过许多家小型粉厂的粉末.绝大多数粉末粒径偏细。平均粒径多在25~32um,<10um的细粉大多在15%左右,而>75um的粗粉又偏少。
过细的粉末流动性很差,超细粉含量高则粉末带电性弱,回收粉量高,粉末利用率降低,喷涂速度也不易提高。相对于高压静电粉末,摩擦枪用粉末更应注重粒径控制,这是因为在摩擦枪中,粉末要带上足够的正电荷,粉末粒子必须以一定的速度与枪管内壁的聚四氟乙烯材料剧烈摩擦。如果粉末粒子太细,与管内壁相摩擦的面积就过小,不足以产生和保持足够的正电荷,摩擦带电喷涂系统中,喷枪和工件之间没有静电场,粉末要沉积到工件上,主要依靠粉末摩擦所带的电荷量,粉末带电量小,静电吸引力低,粉末不易吸附到工件上。经实践观察,<5pm的粉末粒子通常在摩擦枪喷涂系统中无法使用。用于摩擦枪的粉末必须尽量干燥,湿度影响粉末的摩擦带电性。
在生产摩擦枪用粉末涂料时,流动助剂应选用气相法氧化铝。它可增加摩擦带电性。
针对国内粉末厂的许多实际情况,这里列出3种使用方法供大家参考。
(1)若仅生产少量的粉末(如几十或一二百公斤),可将预先计算并称量的气相二氧化硅和粉末半成品机械混合——手工或机器搅拌,然后再进行粉碎。
(2)在粉碎机进料段加开进料口,用专门的气相二氧化硅加料机定量地将二氧化硅加入,完成与挤出半成品的共同粉碎。
(3)在acm磨的空气进风口罩上加开进料口,利用负压,将从气相二氧化硅供料机中输出的二氧化硅吸进磨腔里,与挤出半成品一起粉碎。
控制粉末粒径分布
粉末的粗细从宏观角度考虑应是一个统计学概念,因为成品粉末一定是由粗粉、细粉、以及介于粗粉和细粉之间的粉末构成的。粉末粒径以微米(um)为统计单位,早先采用筛分法进行测定。即称取一定质量的粉末,经过叠加在一起的不同粒径的筛网,统计通过各层筛网的粉末质量,以此来表述该粉末的粒径分布状况。筛分法很费时,每次测试至少要耗时一刻钟,重复性差,数据波动大,现在粉末行业已不再推荐使用。
随着技术的进步,激光衍射粒度分析法已日臻成熟,在国外很早即被用来测试粉末涂料的粒径分布。激光衍射粒度分析法快速方便,可在线检测,通常完整测试一个样品粉仅需2~3min,并能在一个图表中表述一组或几组重要参数和粒径分布曲线图,非常直观。
粉末的粒径分布理论上应呈正态分布(即高斯曲线),反映在图上就是在某个中心点两侧粉末的粒径均匀地减少或增大,在中心点处峰值明显,而且必须是单峰分布。通俗地讲,粉末的粒子大小应尽量集中在平均粒径周围,过粗和过细的粉末粒子都应很少。
粉末的粒径分布从测试图表上来分析应注重以下几点。
(1)平均粒径一般以dv 50表示,这是一个统计概念.即将粉末都看成是一个个直径相等的圆球,其直径的数值以微米(um)为计量单位。
(2)细粉含量也是一个统计数字,意思是小于某个粒径的粉末的累计体积占整个粉末粒子体积的百分比,主要考虑小于10um粒子的百分含量。
(3)粗粉含量同样是统计数字,与细粉含量相对应,主要考虑大于90um粒子的粉末含量
(4)图形分布状况,须观察是单峰还是双峰,峰形高耸还是平坦等。
根据实际经验,这里提供常规粉末的粒径分布参数。
(1)高压静电喷枪用粉末:dv50=35~38um。小于10um的细粉<8%,大于90um的粗粉<3%。
(2)摩擦枪用粉末:dv50=40~45um,<10um的细粉含量<6%,<70 um的粗粉含量>90%。
(3)流化床用粉末:dv50一般在50~60um。<10um的、细粉含量<4%,>170um的粗粉含量<3%。
粉末涂料的喷涂性与细粉含量有很大的关系,细粉(尤其是<5um的超细粉)的带电性能非常差,有时干脆就无法带上电荷。所以这一部分粉末通常会进入回收系统而成为直接的损耗。
曾经测试过许多家小型粉厂的粉末.绝大多数粉末粒径偏细。平均粒径多在25~32um,<10um的细粉大多在15%左右,而>75um的粗粉又偏少。
过细的粉末流动性很差,超细粉含量高则粉末带电性弱,回收粉量高,粉末利用率降低,喷涂速度也不易提高。相对于高压静电粉末,摩擦枪用粉末更应注重粒径控制,这是因为在摩擦枪中,粉末要带上足够的正电荷,粉末粒子必须以一定的速度与枪管内壁的聚四氟乙烯材料剧烈摩擦。如果粉末粒子太细,与管内壁相摩擦的面积就过小,不足以产生和保持足够的正电荷,摩擦带电喷涂系统中,喷枪和工件之间没有静电场,粉末要沉积到工件上,主要依靠粉末摩擦所带的电荷量,粉末带电量小,静电吸引力低,粉末不易吸附到工件上。经实践观察,<5pm的粉末粒子通常在摩擦枪喷涂系统中无法使用。用于摩擦枪的粉末必须尽量干燥,湿度影响粉末的摩擦带电性。
在生产摩擦枪用粉末涂料时,流动助剂应选用气相法氧化铝。它可增加摩擦带电性。